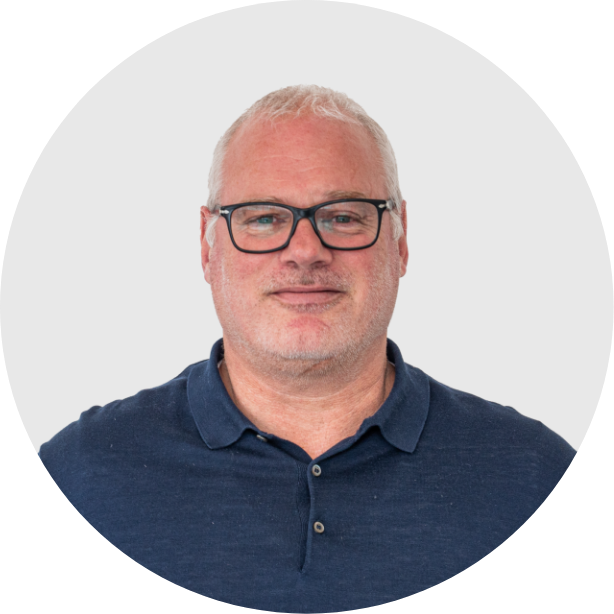
The manufacturing industry is on the move. Innovation and technology are playing an increasing role. For 2025, we see a number of key trends emerging that are changing not only the way companies operate, but also how they add value to their products and services. Below we discuss the four most prominent trends: sustainable manufacturing, smart sensors, robotization and digital twins.
1. Sustainable production
Sustainability is no longer a choice, but a requirement. Consumers and governments are increasingly demanding that companies reduce their ecological footprint. For the manufacturing industry, this means a focus on:
- Circular Economy: Reusing materials and minimizing waste.
- Energy eDiciency: investments in renewable energy sources and eDicer machines.
- Green certifications: Companies that can demonstrate that their processes are sustainable have a competitive advantage.
Sustainable production is not only good for the environment, but also for profitability. It lowers costs in the long run and attracts conscious customers.
2. Smart sensors
Smart sensors are essential to the digitization of the manufacturing industry. They provide real-time data on production processes, allowing companies:
- EDicier ability to work: Problems are detected and solved early.
- Be able to perform predictive maintenance: Machines are maintained before they fail, minimizing downtime.
- Being able to guarantee quality: Through continuous monitoring of production conditions.
The integration of smart sensors leads to higher productivity and lower operating costs. They provide a foundation for other technologies, such as robotics and IoT.
3. Robotization
Robotics remains one of the most transformative technologies in the manufacturing industry. For 2025, we expect a further increase in the adoption of:
- Collaborative robots (cobots): Robots that work alongside humans, especially in repetitive and physical tasks.
- Autonomous systems: Robots that operate independently and make decisions based on data.
- Flexible production: robots that can quickly adapt to new products and production lines.
Robotization increases production capacity, improves quality and reduces labor costs. It also allows companies to safely respond to labor shortages.
4. Digital twins
A digital twin is a virtual replica of a physical product, process or system. Using data and simulations, companies can:
- Optimizing processes: By testing different scenarios without physical resources.
- Accelerate product development: Identify and solve problems before products are actually produced.
- Reduce costs: Less prototyping and eDedicated manufacturing.
Digital twins are becoming especially popular when combined with AI and machine learning, which offer predictive insights and drive innovation.
What do these trends mean for businesses?
The manufacturing industry is on the brink of a new era. Companies that invest in sustainable manufacturing, smart sensors, robotics and digital twins will not only work more eDciently, but also be better prepared for the challenges of the future.
It is essential to take steps now. Consider analyzing current processes, investing in technology and training staff to work with new systems.These trends offer opportunities for growth, innovation and competitive advantage.
Wondering how your company can benefit from these trends? Contact TMC media and find out how we can help you transform into a future-proof manufacturing industry.
Relevant blogs
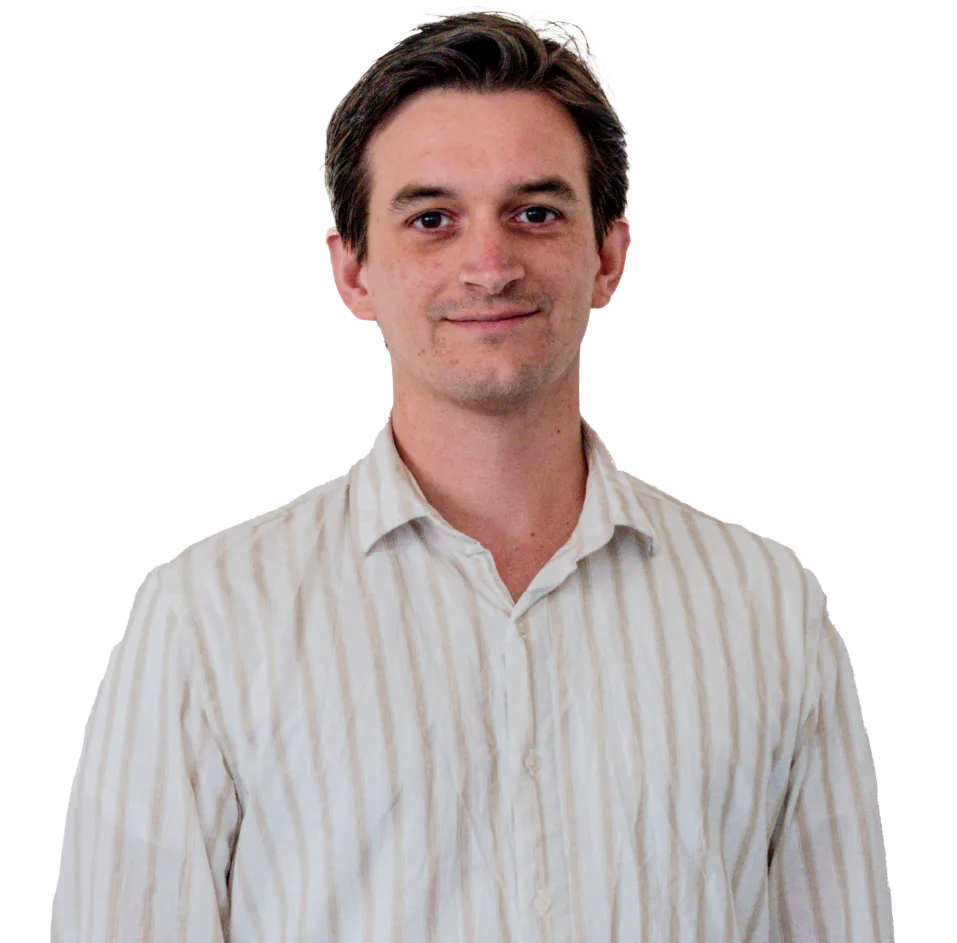
Interested in digital growth for your industry?
Strengthen your online presence and expand your market reach with TMC Media. We combine strategic thinking with innovative creativity for measurable results. From conversion-oriented websites to targeted online marketing campaigns - we are your digital growth partner.
Contact us for a no-obligation consultation